“Smart factory” might sound like the latest industry buzzword, but for manufacturers with their eyes on the future, it’s far more than a trend—it’s a necessity. With the rise of IoT-enabled equipment, AI-powered inspection systems, cloud-based monitoring, and predictive maintenance, the modern production line is evolving at lightning speed. Efficiency is higher, downtime is lower, and decision-making is backed by real-time data.
But amidst all this innovation, one critical question often gets left out of the conversation: Are we simply producing waste faster and more efficiently? In other words, are we automating old inefficiencies instead of solving them?
True smart manufacturing goes beyond speed, automation, and analytics. It’s also about resource intelligence—understanding how to extract maximum value from every pellet, every sheet, every offcut of material. That means rethinking not just production, but what happens after production: how materials are collected, reused, and reintegrated.
In a truly intelligent factory, waste isn’t an afterthought—it’s a data point, a raw material, and an opportunity. By embedding smart recovery systems into your production loop, you’re not just getting leaner—you’re getting smarter where it really counts: at the core of your material flow.
What Exactly Is a Smart Factory?
At its core, a smart factory is more than just a modern production site—it’s an ecosystem where digital technologies continuously monitor, automate, and optimize every aspect of the manufacturing process. Picture a facility where machines talk to each other, systems self-correct in real time, and data flows freely across every department. The key components often include:
- Real-time data capture through IoT sensors and connected devices
- AI-powered quality control that catches defects before they escalate
- Predictive maintenance to prevent breakdowns before they happen
- Robotics and machine learning integrated for precision and agility
- Energy and emissions tracking to meet sustainability goals
These elements work together to reduce unplanned downtime, improve product consistency, and boost throughput—all while offering unprecedented visibility into factory performance.
But here’s the kicker: if your line is still producing large volumes of waste—scrap parts, offcuts, rejects—then there’s a critical blind spot in your digital transformation. Smart doesn’t stop at production speed or predictive analytics. True intelligence means extending those same digital principles to your material management. Because in a truly optimized factory, value isn’t just created at the assembly line—it’s also recovered at the waste bin.
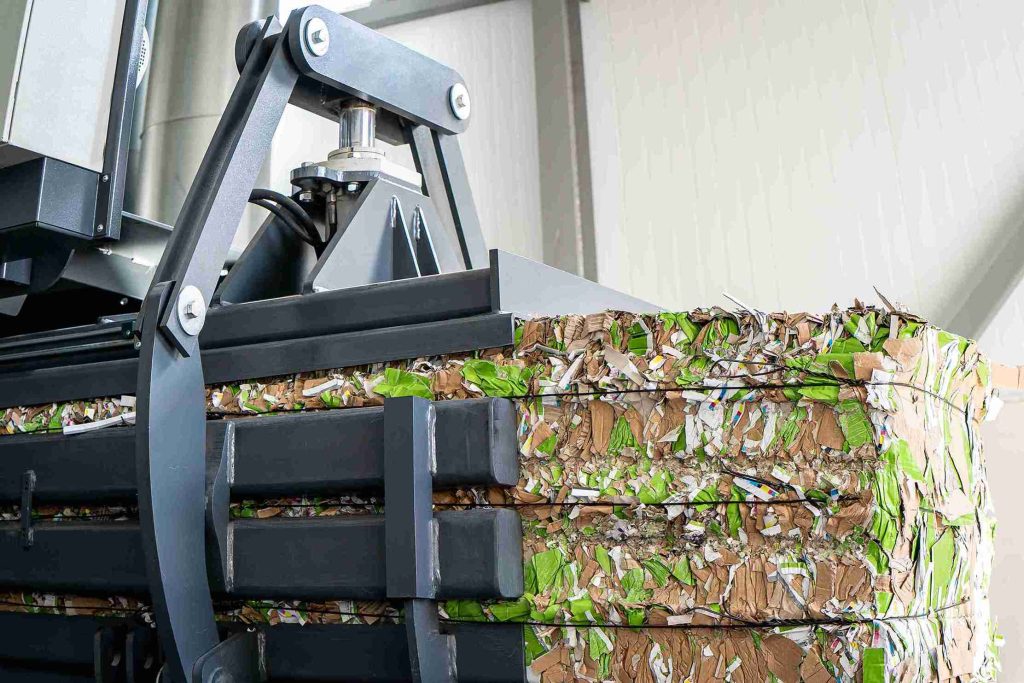
The Overlooked Frontier: Material Recovery
Most smart factory strategies focus heavily on front-end optimization—how to make things faster, more precisely, and with fewer errors. It’s all about refining production flow, automating inspections, and streamlining logistics. But there’s a big piece that often gets overlooked: what happens to the leftovers?
We’re talking about the offcuts, rejects, sprues, and residual plastics that quietly pile up with every shift. They may not show up in glossy upgrade presentations, but they represent a major cost—and a major opportunity.
Instead of paying to store or haul this material away, forward-thinking manufacturers are starting to close the loop on-site. How? By integrating smart, compact mechanical systems that transform scrap into reusable feedstock—right at the source.
Ironically, the tools that enable this shift aren’t flashy AI dashboards or robotic arms—they’re often the underestimated workhorses of the factory: shredders, granulators, and material handling units. But when they’re embedded into a connected system, these so-called “low-tech” machines become powerful enablers of sustainable, cost-effective production.
In short, a truly smart factory doesn’t just produce with precision—it recovers with intelligence, turning yesterday’s waste into tomorrow’s raw material without skipping a beat.
The Smart Role of Shredders in Intelligent Production
Let’s talk plastic shredders—not typically the stars of Industry 4.0, but surprisingly integral to its mission. Modern shredding systems can be equipped with sensors, automatic feeders, and cloud-connected monitoring. They ensure that leftover material is instantly processed and ready for reuse.
When paired with AI-based sorters or dosing systems, plastic shredders help close the loop inside the factory walls. No waste piles. No unnecessary shipments. Just streamlined reprocessing at the point of origin.
One leading appliance manufacturer recently shared how adding shredding stations next to molding machines reduced new resin consumption by 28%—without altering product specs or slowing down operations.
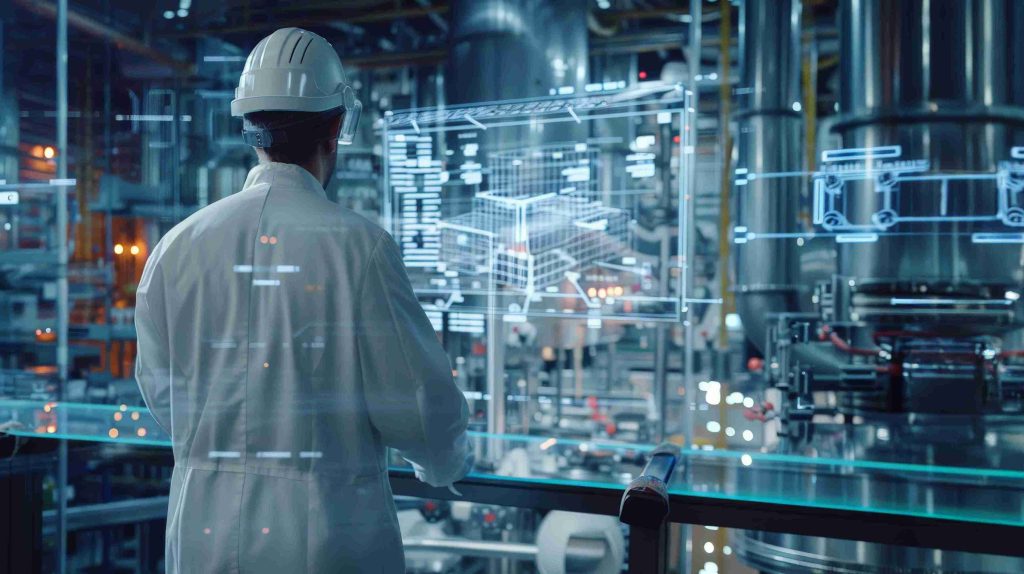
Benefits That Go Beyond Sustainability
Implementing intelligent waste processing doesn’t just reduce environmental impact—it improves your bottom line and strengthens your resilience.
- Cost Savings: Virgin materials are expensive. Reintegrated scraps are nearly free.
- Less Downtime: In-house granulating keeps material flow uninterrupted.
- Compliance: Stricter ESG targets and carbon audits are easier to meet with integrated reuse.
- Data-Driven Decisions: With sensors tracking material use and waste, you gain insights into inefficiencies you didn’t even know existed.
What to Look for in a Smart-Compatible Shredding System
If your factory is getting smarter, your support equipment should keep up. Look for:
– Compact, low-noise shredders that integrate with conveyor belts and hoppers
– Variable output sizes to fit different reprocessing lines
– Cloud or app-based monitoring for remote diagnostics
– Safety interlocks and easy maintenance features
– Modular design for future upgradeability
And most importantly—choose a partner that understands both mechanical reliabilityand digital compatibility.
Conclusion
The most advanced factories today aren’t just packed with robots and sensors—they’re defined by how efficiently they manage their resources. True innovation lies not only in faster production, but in minimizing waste and maximizing reuse. As you evaluate your next round of digital upgrades, don’t overlook the goldmine that’s hiding in plain sight: your production scraps.
Offcuts, rejects, and leftover plastics aren’t just disposal headaches—they’re untapped raw materials. With the right equipment, such as smart-integrated shredders and closed-loop recovery systems, you can turn that waste into reusable input, right on-site. The result? Lower material costs, leaner operations, and a stronger sustainability profile.
This approach isn’t just environmentally responsible—it’s financially strategic. It reduces your dependence on volatile raw material markets and improves your overall process efficiency.
P.S. If you’re planning your smart factory roadmap, start where others stop—at the waste bin. Smart recovery begins with smart fragmentation. With the right systems in place, today’s production leftovers could be your smartest investment yet—and your edge in a market that rewards agility and efficiency.