In recent years, manufacturers around the world have been riding a wild rollercoaster—one fueled by the skyrocketing prices of raw materials. From polypropylene and ABS to PET and PE, the essential plastics that keep factories humming have seen sharp, unpredictable spikes. If you’re in packaging, home appliances, construction, or auto parts, chances are you’ve felt the squeeze firsthand.
So, what’s the hot phrase in every production meeting lately? You guessed it—“cost reduction.” But let’s be honest, slashing costs isn’t as simple as flipping a switch. Sure, you can try to negotiate better deals or tweak your designs, but the real magic happens when you rethink your entire materials strategy. That means not just buying smarter, but using smarter. In this blog, we’ll dive into how manufacturers can take back control—by minimizing waste, maximizing material reuse, and turning overlooked processes (yes, even shredding!) into valuable tools for cost-saving and sustainability.
Is This Price Surge Temporary—or the New Normal?
Let’s take a closer look at what’s really fueling the surge in plastic raw material costs—and why it’s not going away anytime soon.
First up, crude oil volatility. Since most plastics come from petrochemicals, any swing in oil prices sends resin costs skyrocketing. Then there’s environmental policy tightening—governments around the world are clamping down on emissions and limiting high-pollution production, shrinking supply. Add to that the tangle of trade barriers and tariffs, which restrict imports and drive up local prices, especially for specialty polymers.
And let’s not forget the elephant in the room: recycling infrastructure. Or rather, the lack of it. With high-quality recycled plastics still in short supply, manufacturers are stuck relying on expensive virgin resins.
All these forces are creating the perfect storm—and it’s clear this isn’t just a passing phase. So instead of just chasing cheaper deals or cutting corners, smart manufacturers are flipping the script: rethinking how to use materials better, and turning internal waste into a new source of value.
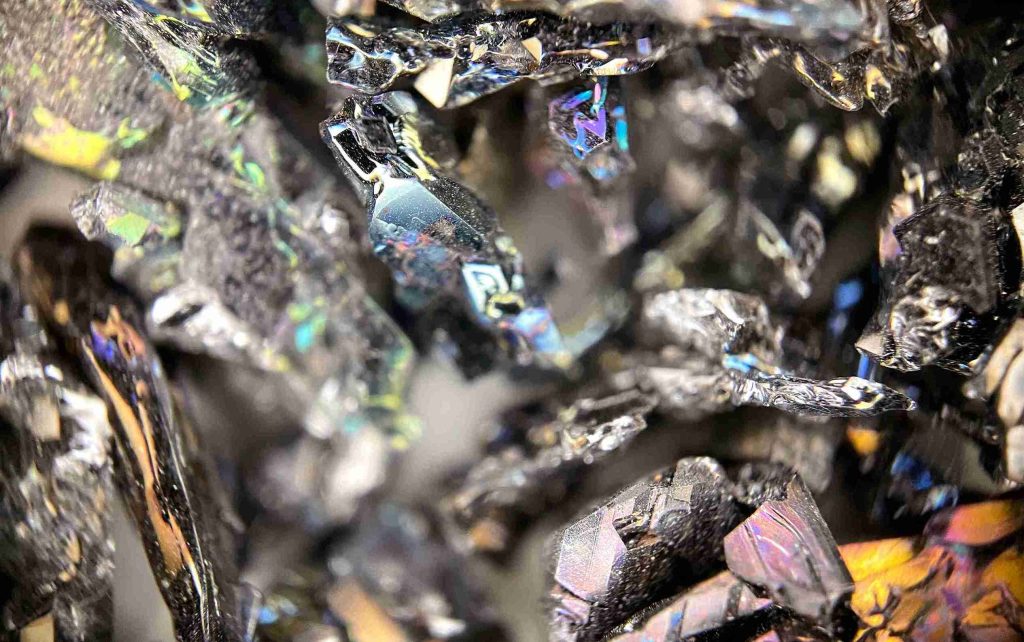
Traditional Cost-Cutting Tactics: Are They Still Working?
For years, manufacturers have leaned on a familiar toolkit to keep material costs in check:
- Supplier Negotiations —Trying to squeeze a little more out of every contract.
- Material Downgauging—Engineering products to use less, without sacrificing performance.
- Alternative Sourcing—Scouting for cheaper, comparable materials wherever possible.
These strategies have their place—but let’s be real: their impact is shrinking. As prices rise across the board, even the best negotiations or substitutions can only go so far. So… what’s next?
It might be time to shift focus inward. Because hiding in plain sight across your shop floor is a massive, often overlooked opportunity: your own production waste.
Think about all those sprues, offcuts, and defective parts. They’re not just trash—they’re assets waiting to be recovered. And more manufacturers are waking up to this. That’s why in-house recycling systems—specifically closed-loop setups—are quickly becoming the new standard.
By capturing and reprocessing your own plastic waste, you create a more efficient, cost-stable workflow. It’s not just a sustainability win—it’s a strategic move that turns yesterday’s losses into tomorrow’s raw materials.
Why Are More Factories Adopting On-Site Shredding?
So, why are more and more manufacturers giving a second look to in-house shredding systems? It’s not just about going green—it’s about getting smart with resources.
- Instant Savings: Let’s start with the obvious—money. By reusing internal waste instead of buying all-new resin, you’re cutting raw material costs straight out of your monthly spend. The more you shred, the more you save.
- Quality Control: Unlike buying recycled material from external suppliers (which can be a mixed bag), shredding your own production waste gives you clean, consistent, and predictable granules. You know exactly what’s going into your next batch.
- Sustainability Wins: Looking to boost your ESG profile? Closing the loop internally reduces your carbon footprint, minimizes waste, and shows your clients and partners that your factory walks the sustainability talk.
- Simple Integration: Think shredders are bulky, complicated machines from the past? Think again. Today’s systems are compact, energy-efficient, easy to operate, and smart enough to sync with your existing production line.
In short, shredders aren’t just for waste—they’re tools for smarter, leaner, greener manufacturing. And the best part? They pay for themselves faster than you’d expect.
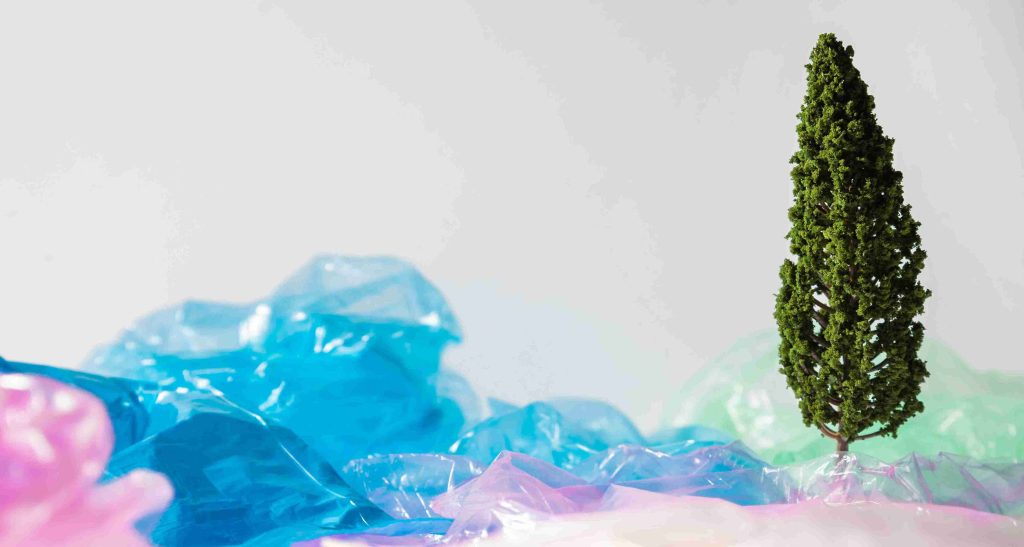
The Underrated Power of Plastic Shredders
Often overlooked, shredders form the backbone of efficient recycling. They transform factory scrap into reusable material—right on the shop floor. One operations manager recently shared, “After integrating shredding systems, 30% of our injection material now comes from recycled in-house waste. The cost difference is major.”
How to Build an Efficient Internal Recycling Loop
If you’re ready to future-proof your factory in 2025 and beyond, consider the following:
- Choose the Right Shredder – Look for speed, consistency, and reliability.
- Go for Automation – Integrated systems reduce labor and maximize purity.
- Sort at the Source – Separate by color and material for quality assurance.
- Connect with Production – Recycled granules can go straight into reprocessing or blending lines.
Conclusion
Raw material prices might keep climbing, but forward-looking manufacturers aren’t just bracing for impact—they’re redesigning their entire approach. In today’s competitive landscape, internal efficiency is the new edge, and that starts with how you handle what used to be “waste.”
Recovery systems are no longer a “nice-to-have” bonus—they’re becoming core infrastructure for cost control and operational resilience. By transforming production scrap into reusable resources right on-site, you’re not only cutting raw material expenses but also building a more agile, sustainable workflow.
Think about it: what if the material you’re discarding could power tomorrow’s production run? That’s not just smart—it’s profitable.
If you’re exploring shredding technology, don’t settle for outdated equipment. Look for solutions that are energy-efficient, easily integrated into your current setup, and low maintenance. Bonus points if it’s smart enough to sync with your digital systems.
Because in modern manufacturing, waste isn’t the end of the line—it’s the beginning of a better, leaner, and more future-ready operation. And in a world where every margin matters, today’s leftovers might just be your next big win.